In the realm of plate heat exchangers, the selection of the right plate material is paramount, especially when dealing with various heat exchange media that differ in corrosiveness. Changsheng Titanium, a leader in the field, emphasizes the importance of choosing materials that not only ensure operational efficiency but also longevity and reliability under different environmental conditions. Here’s an in-depth look at some of the most commonly used materials in heat exchanger plates and their specific applications.
904L and SUS890L Stainless Steel
904L and SUS890L represent austenitic stainless steels known for their excellent balance between cost-effectiveness and corrosion resistance. These materials are particularly adept at handling harsh environments, including exposure to sulfuric acid, phosphoric acid, and halides such as chlorine and fluorine. Their high content of chromium, nickel, and molybdenum enhances their resistance to stress corrosion, pitting, and crevice corrosion, making them suitable for chlorine-containing media.
254 SMO Advanced Stainless Steel
254 SMO is an advanced form of stainless steel that has been improved from type 316 by increasing the molybdenum content. This adjustment grants it superior resistance to chloride pitting and crevice corrosion, making it an ideal choice for saline water and inorganic acids, where traditional stainless steel types might falter.
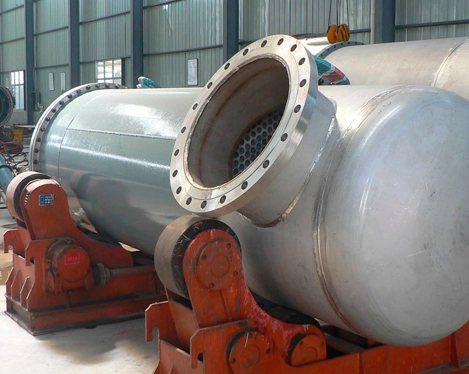
Titanium
Titanium stands out for its exceptional corrosion resistance, especially in chloride-containing environments. Its natural ability to form a passive protective oxide layer (Ti2O3) and its lightweight nature makes it an excellent choice for applications involving seawater and various concentrations of saltwater. Despite its poor resistance to certain acids like sulfuric acid, hydrochloric acid, and hydrofluoric acid, titanium’s overall performance in organic acids and dilute alkaline solutions is noteworthy. Titanium heat exchanger is also a popular choice today! Among Titanium heat exchangers, the titanium coil heat exchanger, titanium pool heat exchanger, titanium plate heat exchanger, and titanium tube heat exchanger stand out for their efficiency and durability. Each type serves a unique purpose, catering to different requirements of heat transfer and fluid dynamics. The titanium coil heat exchanger is often utilized in applications requiring compact solutions and efficient heat transfer in corrosive environments. Its coiled structure maximizes the surface area for heat exchange, making it ideal for space-constrained applications. The titanium pool heat exchanger, on the other hand, is specifically designed for swimming pools and spa heating systems, offering resistance to chlorine and other chemicals present in pool water. Titanium plate heat exchangers are celebrated for their high efficiency and ease of maintenance. Their layered plate design allows for optimal heat transfer between fluids, making them suitable for a wide range of industrial processes. Lastly, the titanium tube heat exchanger, with its robust tubular construction, is perfect for handling high pressures and temperatures, commonly used in power generation and chemical processing industries. Each of these titanium heat exchangers brings forth the benefits of titanium, including corrosion resistance, durability, and efficiency, making them invaluable assets in their respective applications.
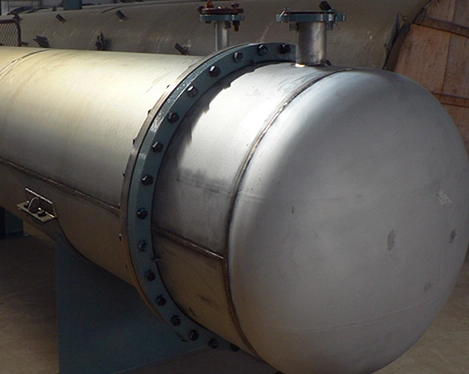
Titanium-Palladium Alloy
Enhancing titanium with palladium (0.12%-0.25%) significantly improves its corrosion resistance, especially in acidic environments. This alloy variant shows excellent resistance to concentrated nitric acid, hydrochloric acid containing oxidizing ions, and plating solutions. It is also suitable for use in dilute sulfuric acid, showcasing its versatility in less demanding conditions.
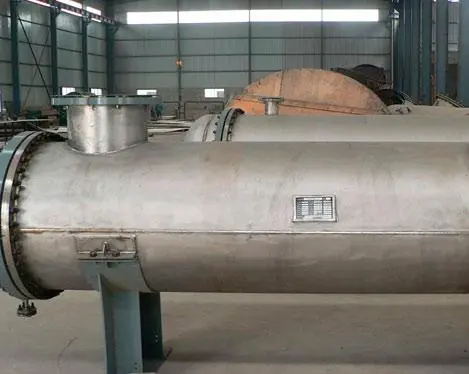
Nickel 200
Nickel 200, characterized by its high purity with over 99% nickel content, is primarily used in environments with highly concentrated caustic alkali solutions. While it offers excellent resistance to such caustic environments, it is susceptible to crevice corrosion in slightly salty water.
Hastelloy C-276
Hastelloy C-276 is renowned for its exceptional corrosion resistance, being almost unaffected by chlorine ions and exhibiting excellent resistance to various concentrations of sulfuric acid. Its application extends to organic acids, high-temperature hydrofluoric acid, and certain concentrations of hydrochloric and phosphoric acids, making it a versatile choice for challenging chemical environments.
Monel 400
Monel 400, a nickel-copper alloy, exhibits good corrosion resistance in specific conditions, such as non-aerated sulfuric acid and hydrofluoric acid, as well as acetic acid and caustic alkalis. It is particularly effective in acidic chloride solutions and offers good high-temperature resistance, although it is not suitable for concentrated sulfuric, hydrochloric, or nitric acids.
Incoloy 825
Incoloy 825 performs well in various sulfuric acid concentrations at low temperatures and demonstrates good corrosion resistance in caustic alkali solutions. However, its sensitivity to crevice corrosion caused by chlorides and less than ideal stamping performance limit its widespread use as a plate material.
Conclusion
The choice of plate material in heat exchangers is a critical decision that impacts the efficiency, durability, and application suitability of these systems. From the corrosion-resistant and cost-effective 904L and SUS890L stainless steels to the exceptional durability and efficiency of titanium and its alloys, each material offers unique benefits tailored to specific environmental conditions and process requirements. Changsheng Titanium’s expertise in providing high-quality materials ensures that industries can leverage these advanced materials for efficient, sustainable, and cost-effective heat exchange solutions.